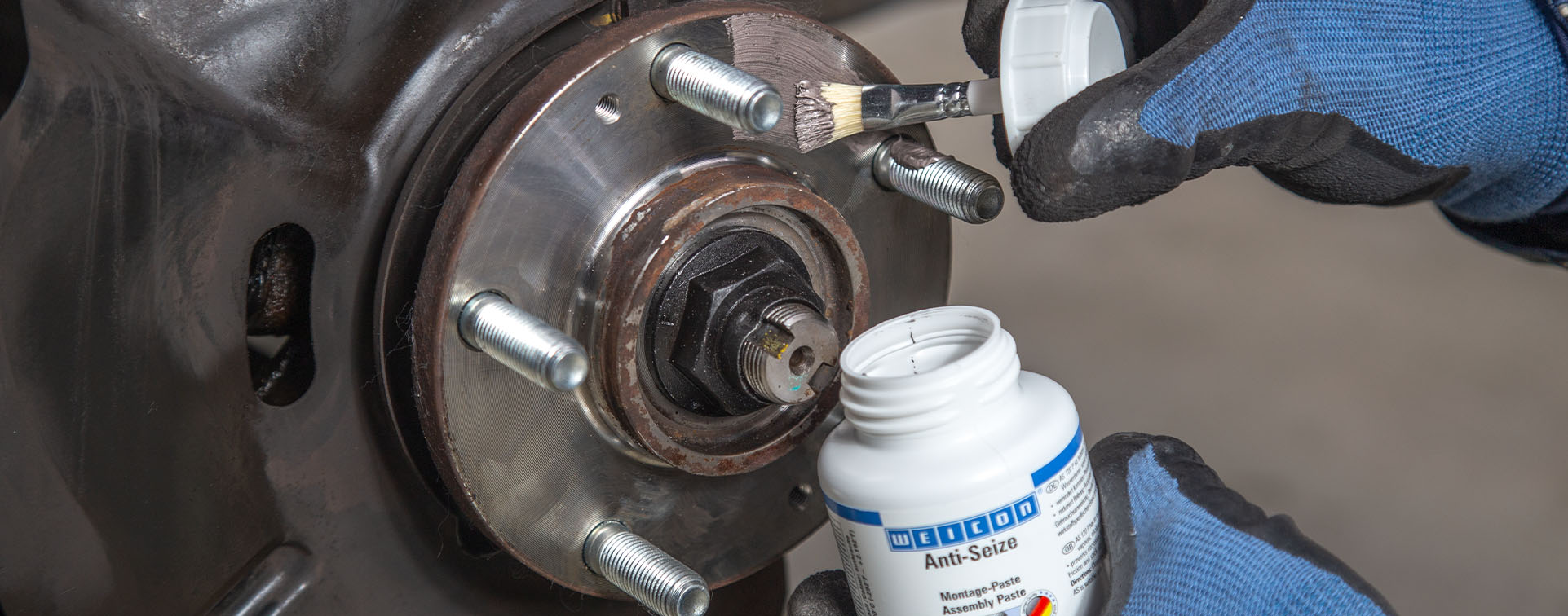

What are lubricants?
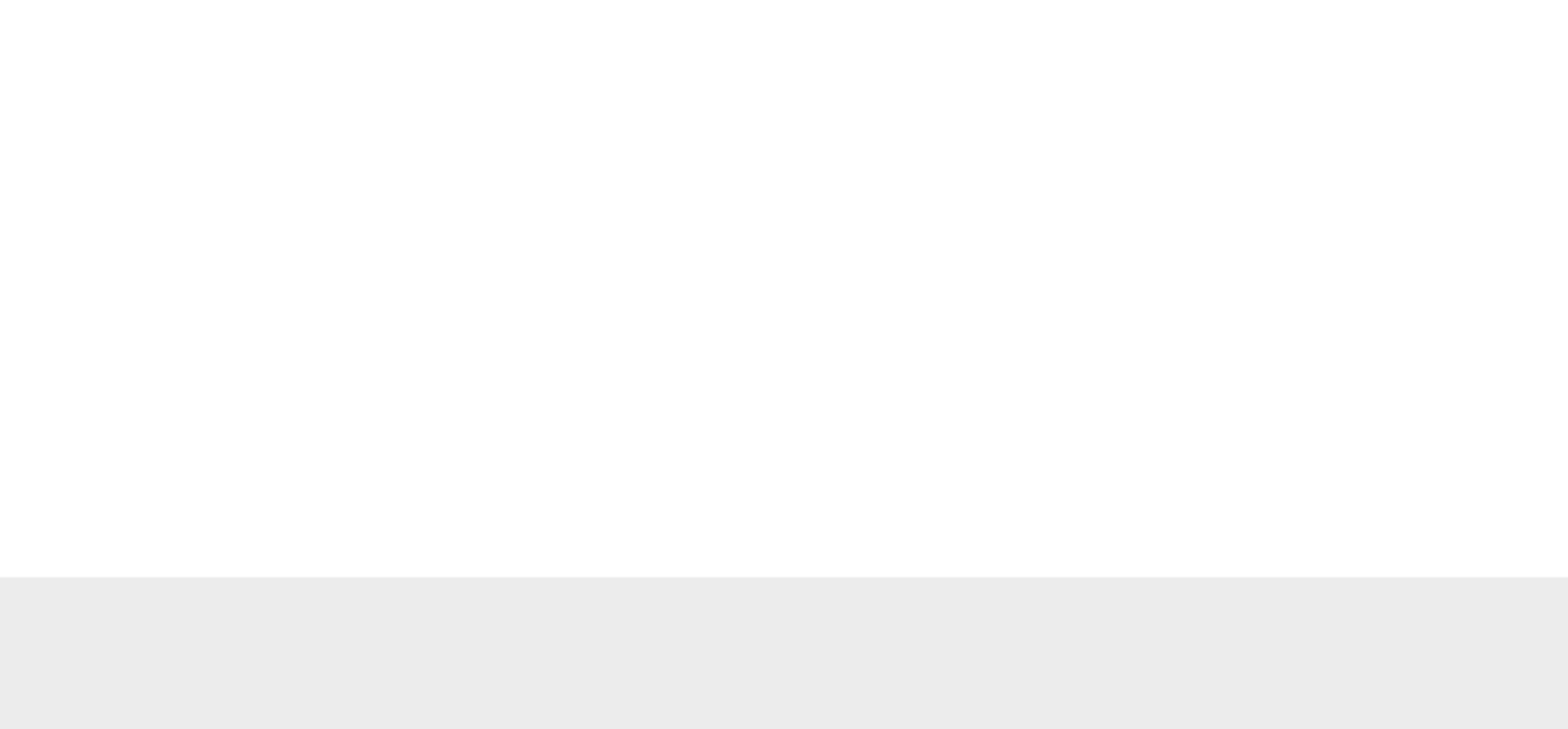
First and foremost, lubricants protect against wear. Wear is caused by the permanent movement of two parts against each other and the friction involved. As a result, the surfaces wear off, which leads to a material loss. In addition, chemical and thermal stresses can also cause wear. Therefore, lubricants are indispensable helpers in many industries and are used for a large number of components and machines. Lubricants can be divided into the different types of lubricating oils, greases, lubricating pastes and dry lubricants.
Lubricants are used to build up a separating layer and thus to reduce friction between two components that move against each other. They support power transmission, ensure sufficient heat supply or cooling, dampen vibrations, and are able to seal systems and protect against corrosion.
After some time, lubricants wear out and need to be reapplied at regular intervals. The manuals of the machine manufacturers provide information on the intervals at which relubrication is required. Operating machines over longer periods of time with used up lubricant can cause damage and even machine breakdowns.
Generally, choosing the right lubricant depends on the individual requirements and particularly on the construction of the machine and its field of application and operating mode. The basis of the lubricants provides information about their basic characteristics and their miscibility.
What are lubricants?
Lubricants and multifunctional oils have a high base oil content. The advantage of lubricating oils is their very fine lubricating film. Due to their low viscosity, lubricating oils are ideal for spaces on machines that are difficult to access. In addition, they have a cooling effect and remove soilings. They withstand high rotation speeds on gears, chains and bearings very well.
to see our lubricating oils.
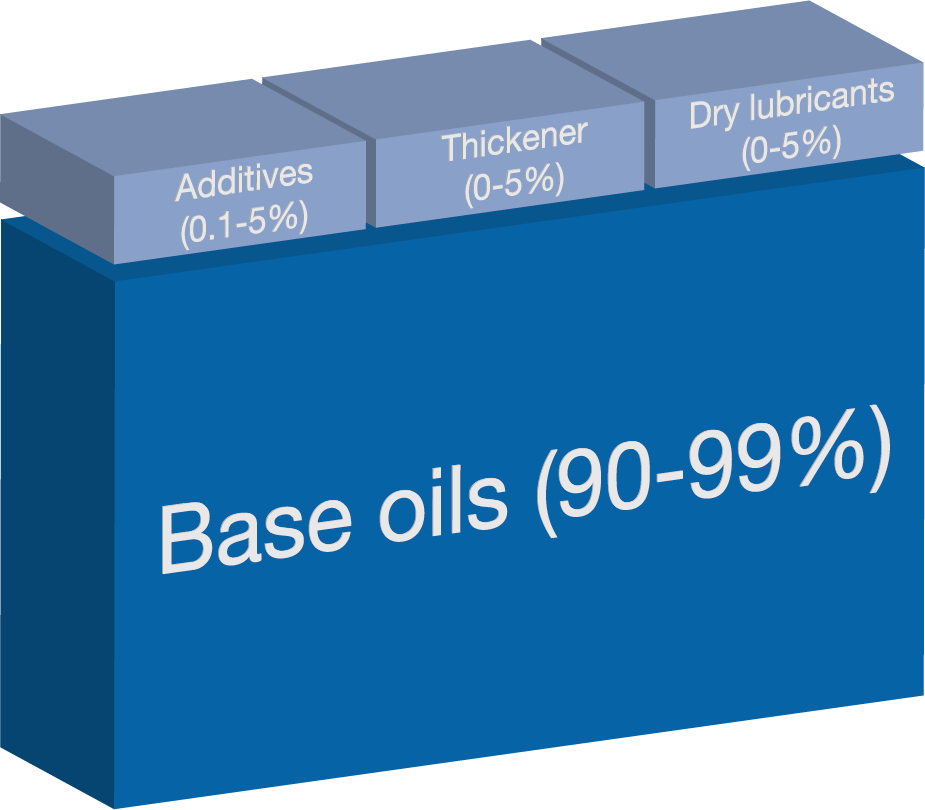
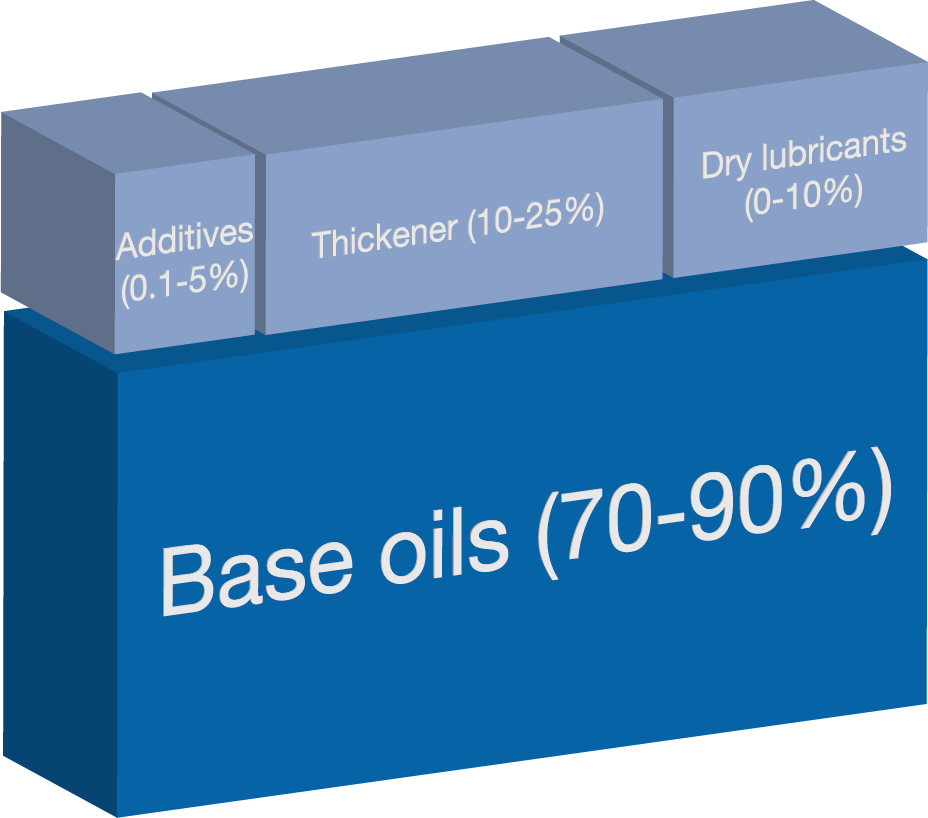
What are greases?
Greases have a higher viscosity compared to solvents and do not run, which is why they adhere better and longer to the friction point. Greases have a particularly high pressure stability and are used when high forces act on the surfaces with low speeds. This happens, for example, on joints, levers, sliding guides, spindles, shafts, or rolling and plain bearings. Lubricating greases also consist to a large extent of a base oil, combined with thickeners and additives.
to see our greases.
What are assembly pastes?
Assembly pastes, in contrast, have a high content of solid lubricant - usually between 30 and 50 percent. This means they are ideally equipped for high operating temperatures, high pressure loads or permanent outdoor weather conditions. They protect against oxidation, corrosion, fretting corrosion, stick-slip effects and "cold welding". Assembly pastes are used where little to no movement happens, but very high forces act. That is why they are the ideal lubricant for screw joints or pressing in pins and bolts. They ensure that screw joints "stick", but that they can still be disassembled at any time.
to see our assembly pastes.
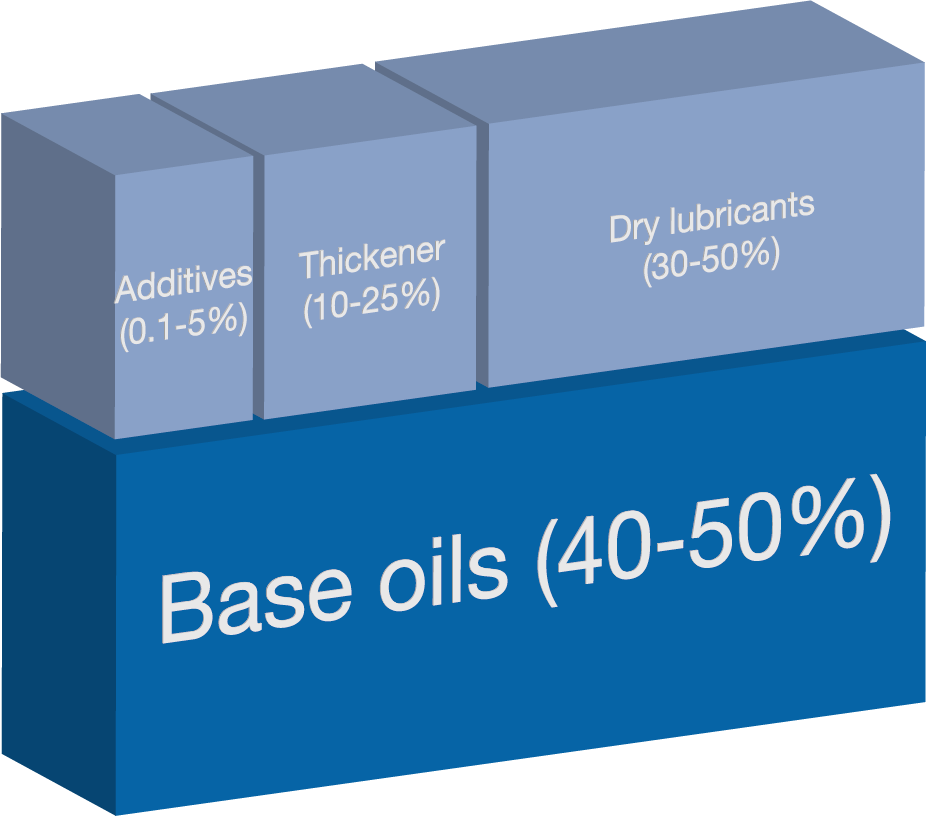
What are dry lubricants?
In addition, there is also the group of dry lubricants. They can be divided into powdered solid lubricants, wax-like sliding films and solid-containing bonded coatings. Dry lubricants also form a very thin, dry and tightly adhering lubricating film. They have a high pressure resistance and prevent dirt from adhering. They also protect against stick-slip effects, facilitate assembly and disassembly, protect against corrosion and reduce machine noise. One example is our Anti-Friction Spray MoS2. MoS2 is a soft mineral, which ensures high pressure resistance when contained in grease. The spray can be used, for example, on open sliding surfaces that are exposed to dust, on conveyor belts and wherever oil or grease lubrication is not permitted or desired.
What are the advantages of the right lubrication?
✓ increased productivity, quality, reliability and sustainability
✓ reduced energy and operating costs
✓ higher machine availability due to longer maintenance intervals
✓ low wear and thus minimised downtimes
✓ reduction of noise due to friction
✓ longer service life of machines and systems
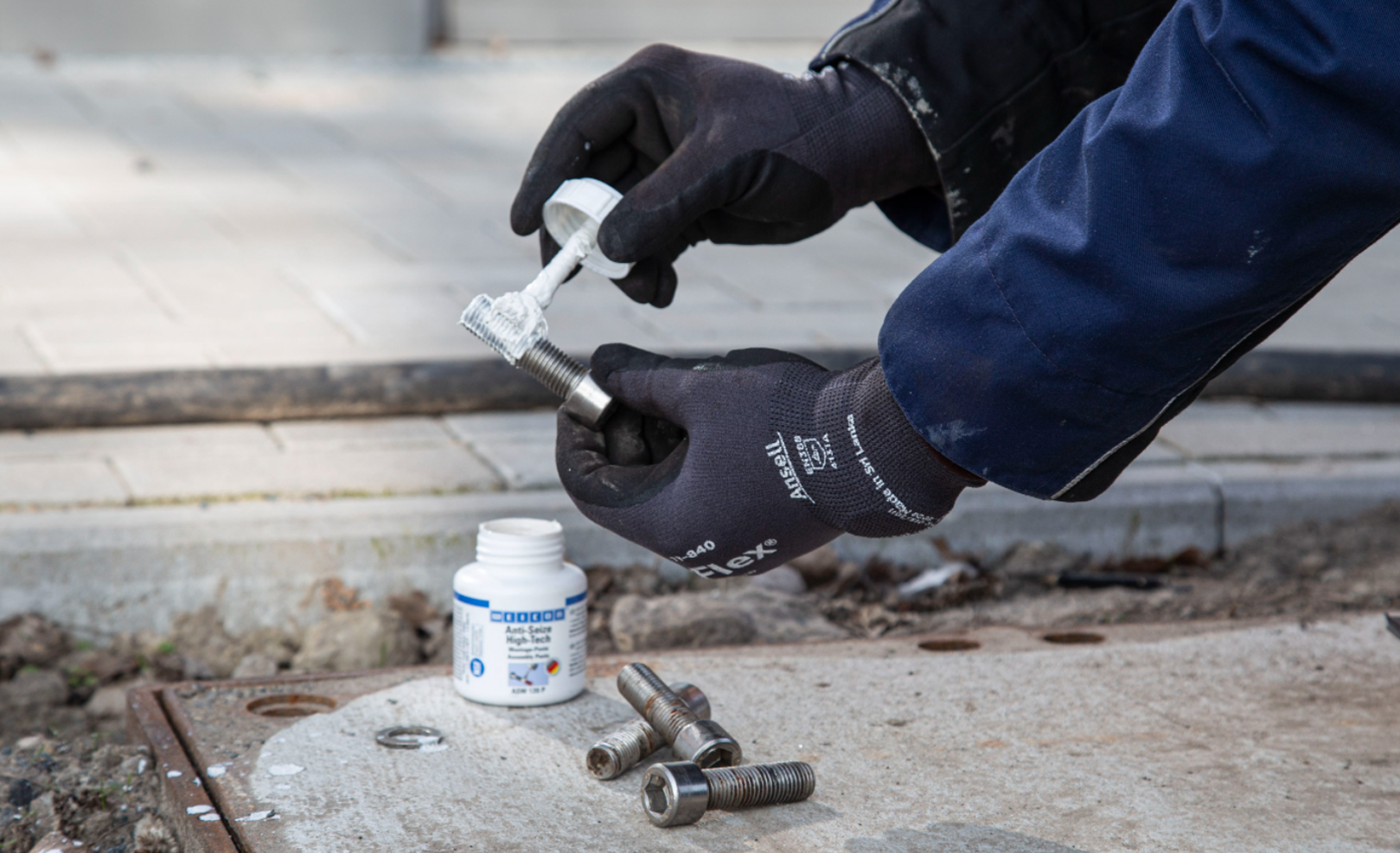
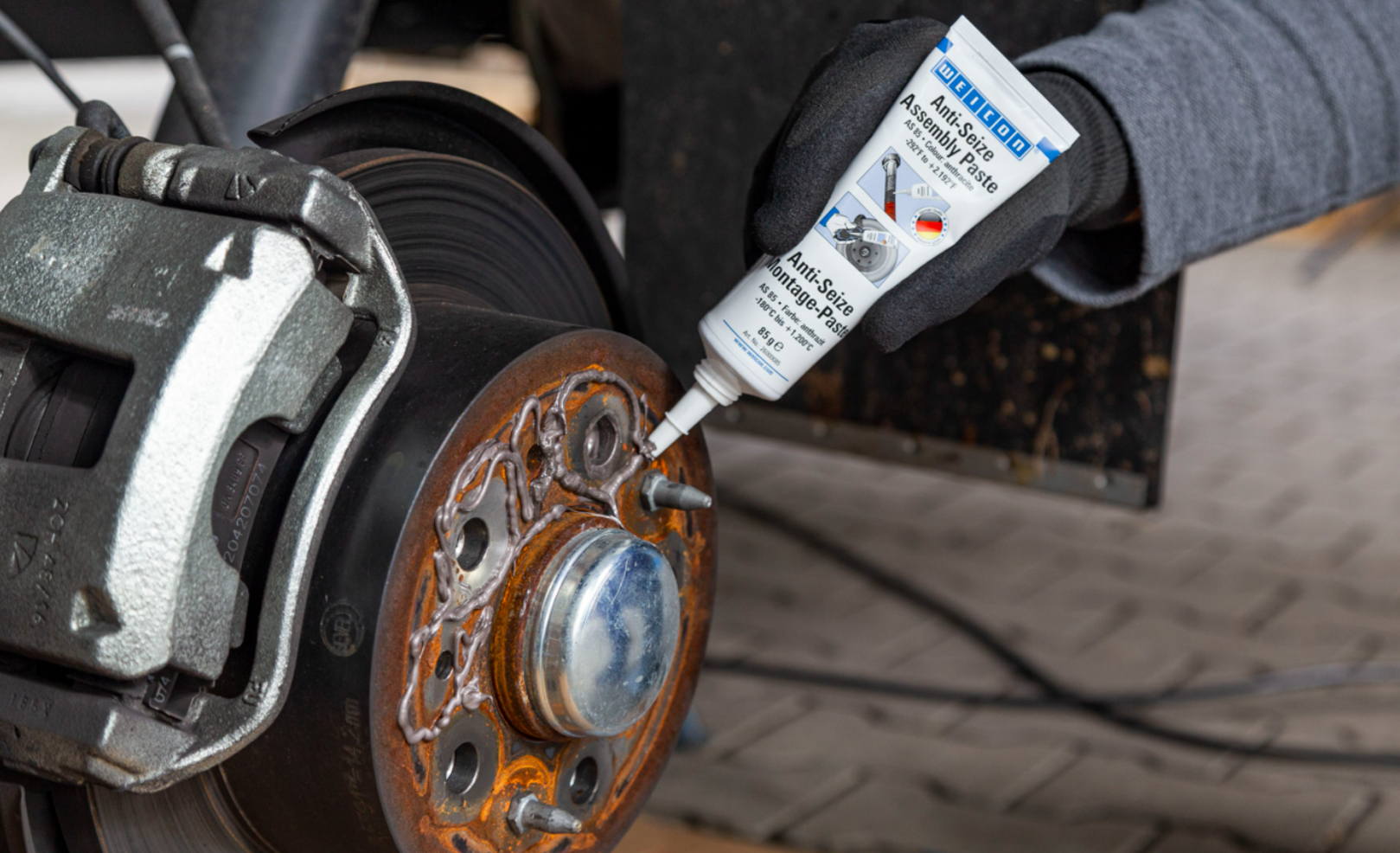